How to Cut Wait Times in a Busy PC Repair Shop
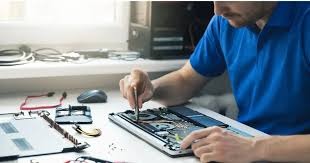
What’s the single most annoying thing that customers hate? Wait times! If you truly care about your customers and want them to keep returning to your repair shop, cater to their needs quickly. But not many do that. According to research conducted by Harris Poll, working Americans lose nearly 31 hours each year sitting on hold or waiting for service technicians. So, what should you do to cut wait times? Well, for starters, tighten triage at check-in, organize benches, and let the computer repair shop software move tickets automatically. Here are a few more tips that will allow you to serve your customers better without making them wait too long.
-
Diagnose Right the First Time
Every minute spent guessing at the counter is a minute the next customer waits. Give each device a quick triage the moment it lands on the mat. Plug in a known-good power cord, hit the power button, and note any beep codes or fan spin. If the machine boots, move to a fast health check and run built-in diagnostics. Open the task manager and watch temps. No boot? Pop the side panel and look for loose RAM or a blown capacitor. Photograph screen messages and board damage, then attach them to the ticket so every tech sees the same clues. A standard checklist cuts repeat trips to the front desk and stops needless part orders. Print the sheet, tape it beside every station, and train new hires to follow it step by step. When the first look is reliable, the whole queue moves faster.
-
Organize Bench Layouts and Parts
A cluttered bench drains time fast. Group your most-used tools like Phillips drivers, Torx bits, pry tools, and thermal paste within arm’s reach on a pegboard or magnetic strip. Keep screws sorted by size in clear, labeled trays: one tray for laptop shells, another for motherboard mounts, another for drive cages. Store common parts like SATA cables, Wi-Fi cards, and thermal pads in small bins marked with big, legible tags. When every item has a fixed spot, techs stop digging through drawers and asking each other where the 2 mm standoffs went. Sweep the bench nightly, restock trays, and toss worn bits so they don’t creep back into use. A tidy layout turns mere seconds saved per step into hours gained each week, and that freed-up time means shorter lines and happier customers.
-
Use Clear Job Slots and Timers
Confusion over “what’s next” stalls every bench. You should divide your day into different job slots. For instance, you can pick morning for quick diagnostics, midday for repairs waiting on parts, and late afternoon for pickups and quality checks. You can also mount a big countdown timer or a simple traffic-light board above the benches. Green will indicate jobs that are active, yellow will be for waiting parts, and red for needing review. Better yet, let the computer repair shop software update the board automatically. When a ticket moves from “diagnosis” to “repair,” the screen flips the color and pings the assigned tech. Clear visual signals and auto-updates shave minutes off each hand-off, keep tasks flowing, and prevent idle gaps that stretch customer wait times.
-
Keep Customers in the Loop
Silence makes people anxious. If days pass by and you don’t give any status update to your customers, they might call or show up at the store and clog the counter. And guess what, every such interruption will slow down repairs for everyone. Therefore, send out an email or a text message at three important times: one, when the PC arrives on the bench, two, when parts are ordered, and three, when the final test passes. A clear message can be as simple as “Diagnostics done, bad drive, new one arrives tomorrow.” You can also post turnaround targets on the front desk so that the client’s expectations match reality. When your customers feel informed, they wait calmly, trust your process, and pick up on schedule, keeping the queue clear for the next job.
-
Offer Fast-Track Services
Not every fix needs a full overnight stay. Set up a “while-you-wait” lane for quick wins like RAM swaps, fan clean-outs, or antivirus removals. Advertise a flat, slightly higher fee and a strict 30-minute target. Reserve one bench, a spare blower, and common parts just for these express jobs. Fast track keeps simple repairs from clogging the main queue, frees space for deeper motherboard work, and gives customers a pleasant surprise like coffee or a short chat. It is advised to track express tickets separately so you can see exactly how many walk-ins turn into quick revenue without derailing bigger projects.
Final Thoughts
Shorter waits come from small daily habits. Start with a solid triage, keep the bench tidy, post a live queue, keep clients updated, and reserve an express lane. Link each habit to your ticketing board inside computer repair shop software, and the plan runs itself. Jobs move in a clear order, parts stay visible, and techs spend less time hunting or answering repeat calls. Put these steps to work today and watch feet move through the doorway faster, service rates climb, and customer smiles stick around for the next visit.