Business Improvement Techniques: Proven Strategies to Optimize Performance and Achieve Operational Excellence
Unlock growth with effective methodologies like Lean, Six Sigma, and Kaizen for continuous process improvement.
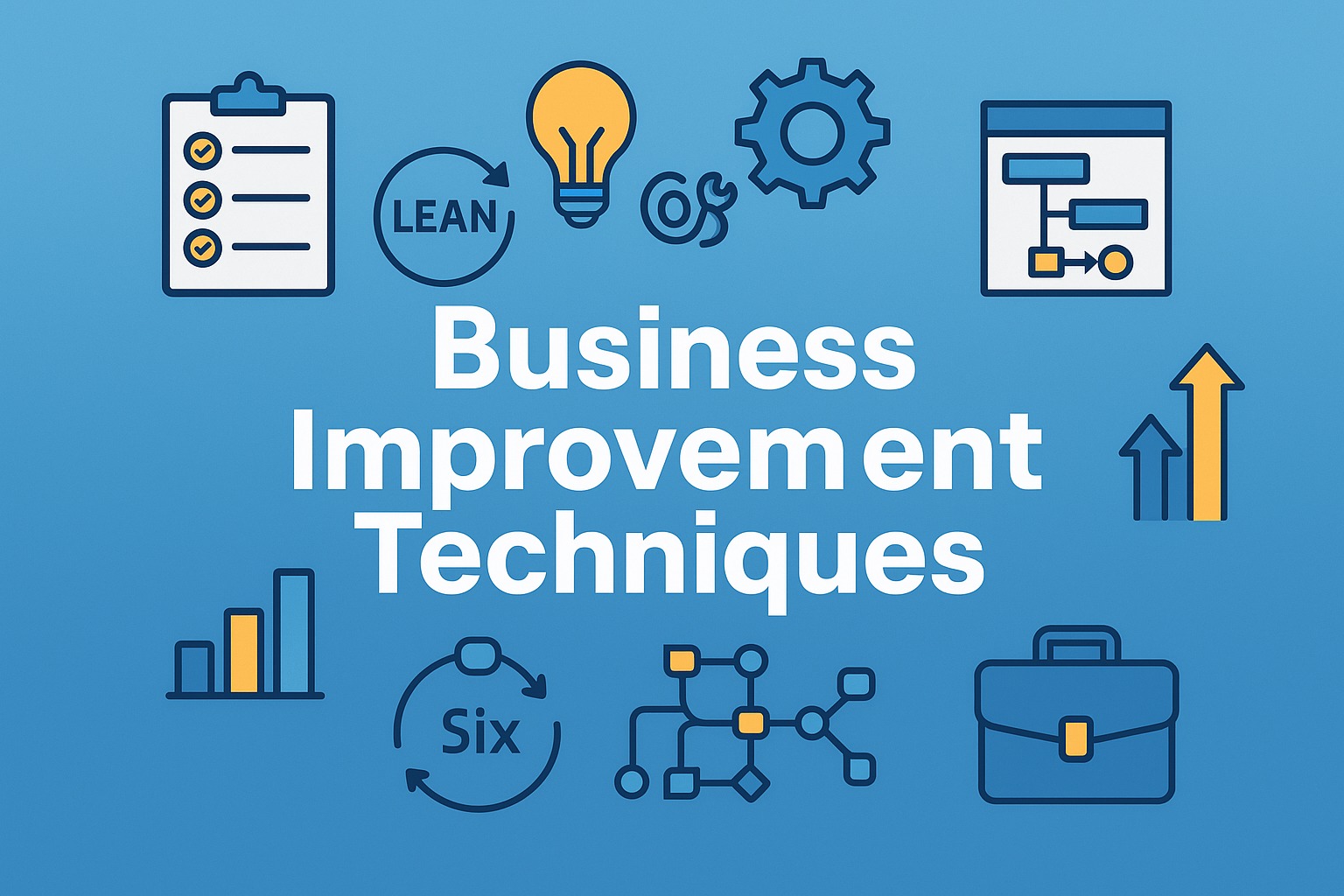
Introduction
In today’s competitive environment, organizations must continuously improve their operations to stay relevant, efficient, and profitable. That’s where business improvement techniques come into play. These strategies help companies enhance productivity, reduce waste, and optimize workflow. Whether you’re in manufacturing, healthcare, finance, or customer service, applying the right business process improvement approach can lead to significant gains in quality and performance.
This article explores the most effective business improvement techniques, breaking down methods like Lean management, Six Sigma, Kaizen, and others. You’ll also discover how tools like Value Stream Mapping (VSM) and Root Cause Analysis (RCA) can support your journey toward operational excellence.
What Are Business Improvement Techniques?
Business improvement techniques are structured methods used to identify inefficiencies, optimize performance, and ensure continuous development in business processes. These strategies aim at enhancing productivity, quality, and customer satisfaction while minimizing costs.
Why Are They Important?
-
Improve operational efficiency
-
Enhance customer experience
-
Increase employee engagement
-
Support cost reduction strategies
-
Drive organizational development
Core Business Improvement Methodologies
1. Lean Management
Lean management focuses on eliminating waste while maximizing customer value. Originating from the Toyota Production System, this method encourages a culture of continuous improvement and problem-solving at every level.
Key Principles of Lean:
-
Identify value
-
Map the value stream
-
Create continuous flow
-
Establish pull systems
-
Strive for perfection
Used in both manufacturing process improvement and service quality enhancement, Lean drives workflow automation and process simplicity.
2. Six Sigma and DMAIC
Six Sigma is a data-driven technique that aims to reduce defects and variability in processes. It uses the DMAIC framework:
-
Define the problem
-
Measure key aspects
-
Analyze data to find root causes
-
Improve processes
-
Control to sustain improvements
Six Sigma often overlaps with Lean as Lean Six Sigma, blending speed and accuracy.
3. Kaizen (Continuous Improvement)
Kaizen means “change for better” in Japanese. It promotes small, incremental improvements involving every employee—from the CEO to the shop floor.
Benefits of Kaizen:
-
Boosts employee morale
-
Encourages team collaboration
-
Reduces waste and inefficiencies
Kaizen contributes to a culture of business excellence through consistent and proactive enhancements.
4. Total Quality Management (TQM)
TQM is a long-term approach that focuses on customer satisfaction through continuous improvement in products, services, and processes.
TQM Practices Include:
-
Employee involvement
-
Continuous training
-
Standardized processes
-
Quality-focused leadership
TQM is widely used in healthcare process improvement and financial process improvement sectors.
Essential Tools and Techniques
5. 5S Methodology
A system for workplace organization based on five Japanese words:
-
Sort, Set in order, Shine, Standardize, Sustain
5S boosts productivity enhancement and maintains efficiency in both office and production settings.
6. Root Cause Analysis (RCA)
RCA is used to pinpoint the root cause of problems, enabling organizations to solve issues permanently rather than just treating symptoms.
Common RCA Tools:
-
Fishbone (Ishikawa) diagrams
-
5 Whys analysis
-
Fault Tree Analysis
RCA is crucial for quality management and process optimization.
7. Value Stream Mapping (VSM)
VSM is a visual tool used to map all steps in a process and identify non-value-adding activities.
Applications of VSM:
-
Supply chain optimization
-
Service delivery analysis
-
Operational improvement
8. Plan-Do-Check-Act (PDCA) Cycle
Also known as the Deming Cycle, PDCA is an iterative process used for performance improvement.
-
Plan: Identify opportunities
-
Do: Implement a solution
-
Check: Measure the outcome
-
Act: Adjust and standardize
9. Business Process Reengineering (BPR)
BPR involves radical redesign of processes to achieve breakthrough results in efficiency improvement and cost reduction strategies.
10. Agile Methodology
Agile emphasizes flexibility and collaboration, ideal for tech-driven projects. It promotes rapid development cycles, feedback loops, and adaptability—ideal for dynamic sectors.
Supporting Concepts and Practices
Benchmarking
Compare your processes and metrics against industry leaders to identify improvement opportunities.
Poka-Yoke (Error-Proofing)
Design processes in a way that prevents errors before they occur.
SIPOC Diagrams
Visual tools showing Suppliers, Inputs, Processes, Outputs, and Customers to clarify scope.
Standard Operating Procedures (SOPs)
Ensure consistency by documenting how to perform routine business activities.
Gemba Walks
Managers observe work processes on-site to identify improvement opportunities firsthand.
Real-World Applications
These techniques are applied across industries:
-
Manufacturing process improvement
-
Healthcare process improvement
-
Financial process improvement
-
Customer experience improvement
-
Service quality enhancement
Whether it’s reducing waste in a factory or improving billing accuracy in a hospital, these techniques are versatile and effective.
FAQs – Business Improvement Techniques
Q1: What is the most effective business improvement technique?
It depends on your goals. Lean is best for waste reduction, while Six Sigma is ideal for reducing variation.
Q2: How do I choose the right technique?
Conduct a process mapping or RCA session to identify pain points, then apply the method that aligns with your goals.
Q3: Can these techniques work for small businesses?
Yes, especially Kaizen, 5S, and PDCA, which are low-cost and highly adaptable.
Q4: How often should we review improvement strategies?
Regularly—ideally every quarter. Use benchmarking and performance metrics to assess progress.
Q5: What’s the difference between continuous improvement and business process reengineering?
Continuous improvement focuses on small, ongoing changes, while BPR involves major overhauls to business systems.
Conclusion
Implementing the right business improvement techniques can transform your organization. From Lean management to Agile methodology, these strategies enable smarter decision-making, reduce inefficiencies, and build a culture of continuous improvement. Whether you’re aiming for cost reduction, process optimization, or organizational development, using these tools will help you compete and thrive in any industry.